Warehouse Space Utilization
Warehouse Space Utilization
- share
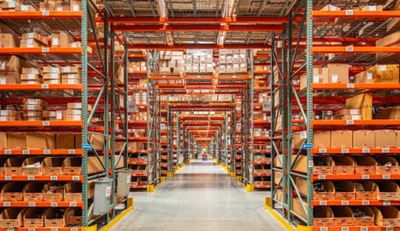
Associated University takes an in-depth look at various strategies to optimize your space though process and automation applications.
Warehouse Space Utilization
In any given warehouse facility, optimizing space revolves around finding the ideal distribution between your three primary functional areas: material storage space, traffic space and working space. Traditional warehouses designed with single-depth pallet racking and manual packing stations can be considered less efficient because of the relatively large amount of square footage allocated for traffic and work areas.
This results in a smaller proportion of the overall space being available for material storage than would otherwise be possible. High-volume modern warehouses, on the other hand, look to maximize storage density (while minimizing traffic and work areas) through the use of automated equipment and engineered work practices. Between these two examples, we can gather that the goal of optimizing warehouse space utilization is finding the highest density storage footprint and smallest traffic / work areas needed to serve your specific overall material volume, at the price and complexity point that best meets your needs.
Work Practices
-
Standardize Tasks
-
Any space optimization discussion should always start with standardization. Employees and management should be fully aligned on work procedures, performance expectations, and overall business priorities. From that starting point, work- and space-use efficiencies can be embedded throughout. Mapping specific storage positions, defining traffic patterns, and assigning discrete job duties all help manage down risks of waste.
Standardization is half an effort in formalizing and documenting work steps, and half an effort in training, positive reinforcement, and in-place coaching. While this might not be an easy road to venture down, especially in companies where formal procedures have not been used prior, the benefits of calibrating employees in the direction of deliberate, consistent working decisions sets the stage for the rest of the optimization efforts to come. -
Staging Buffers
Anywhere in your warehouse that you find bottlenecks, delays, or idle workers, you likely have a good spot to add staging buffers. Staging effectively decouples work processes, providing a buffer such that a hiccup in one work step won't immediately impact other steps. This can be as simple as requiring a certain quantity of materials stated at the dock before the truck is backed in and helps optimize space utilization by reducing work-in-progress piles driven by delays in finishing tasks.
The remaining manual element is simply that the operator needs to walk with the truck and steer with their arms – the electric travel and lift motors do the rest. Similar to manual pallet jacks, motorized hand trucks can only elevate pallets several inches off of the ground, ideally used for moving heavy, high-volume materials around at ground level. -
Manage by Data
In distribution, manufacturing and warehousing operations, managerial metrics are particularly important to both implement and leverage continuously. Wasted storage space is often the result of inefficiencies that might not be immediately discernible. Receiving excessive partial deliveries, having long periods between return shipments, and keeping dead inventory too long are examples of space losses that can be readily identified in data metrics.
In our current logistics climate, several warehouse metrics might be of specific interest to look into, even though they at first will appear to fall on the opposite end of a space utilization conversation. - Backorder Rate may initially be dismissed from contributing to space inefficiency as in concept, we’re not discussing a material we have in hand taking up space. However, if warehouse managers are holding excessive open storage positions awaiting backordered materials (as in the usual bins or pallet spots that hold these materials), there is likely valuable real estate sitting empty that could be utilized in the meantime.
- On-Time Delivery rate is another sneaky metric that might be hiding space-saving value. If managers are in the habit of pre-building truck loads and staging early (to hit good delivery rates), you might be storing materials “twice” – one partial storage position where a product was just picked from, and another partial storage position where the order lot sits awaiting a truck.
Material Workflow
-
Space Adjacency
Warehouse designs should embody minimal travel distances between work steps, which is known as the process of evaluating adjacencies. Placing sequential work steps 'adjacent' to each other cuts out unnecessary forklift and foot traffic space, freeing up area for more valuable uses. This can further translate into adjacent rooms, adjacent equipment positions, adjacent supplies, and so on – any improvements that can render more functional time and space (by reducing the need for travel) is a benefit to overall space utilization.
This unique extension capability works with rack designs that are 2, 3, or more pallets deep, which cuts down on the amount of traffic aisles needed between stored materials, and in turn increases overall storage density. -
Velocity-Based Organization (Zone Picking)
In space planning, the above adjacency evaluation is often immediately followed by velocity evaluation. In short, velocity-based storage organization works to locate materials in the warehouse based on how frequently they need to be accessed. High-velocity products end up close to packing stations in order to reduce the time needed to pull them, which can also suggest higher density storage and higher-volume traffic lanes just in these areas.
For creative managers, the concepts of physical adjacency planning and velocity-based organization tend to stimulate adjacency-based thinking as well. When looking at workflows and procedures (especially when accompanied by the workflow standardization described above), excessive travel is often found to be baked into established processes as a function of completing a sequential task over a non-sequentially organized space. For example, an employee might receive a pick order that follows SKU numbers but requires walking down the same aisle three times, instead of picking adjacent SKUs in one trip even if they’re out of order on the pick ticket. We find opportunities here to start recreating workflows to take advantage of inefficient processes, such as single-order picking which can be replaced with batch picking. -
Conveyance
-
Carrying workflow optimization one step further, designers can employ material conveyance solutions between adjacent, high-velocity material paths that serve to replace the space otherwise needed for transport vehicles (forklifts, push carts) with more storage. Conveyors can be installed overhead, saving more space, and can even serve as passive accumulation space as we described above (the conveyor itself ‘accumulates’ materials as they are in transit, providing an indirect buffer space of sorts).
This topic will carry us into the next category of discussion around automated solutions, but first, we offer a few other thoughts on simple powered conveyance technology. It’s often assumed that conveyance applies to packaged goods only (IE, filled boxes ready to ship), when in fact, there are economical solutions out there for virtually any material that needs transportation in a warehouse. Installing conveyance for flat cardboard inserts, labels, erected empty boxes, and even filling material can all work in the direction of reducing traffic space, freeing up warehouse areas for more valuable uses.
Conveyance doesn’t have to be a linear conveyor only. For label conveyance, we often see overhead mezzanines installed to store label rolls, which are then conveyed vertically via small vertical elevators to the packing lines below. For fill material, pneumatic or auger conveyance can be used to move fill from a bulk unloading station out to the packing lines. Combining this concept with adjacencies, managers might find that they can now rearrange storage space in unique ways, such as moving cardboard storage to a low-ceiling height part of the facility and conveying it to the lines, while repurposing the previous space for additional tall product racks closer to the shipping dock.
Automated Technologies
-
Individual Task Machinery
Work areas that house a high quantity of employees performing manual tasks tend to be excellent candidates for deploying automated equipment. Machinery helps reduce the area needed for workers and materials, improves work speed, and frees up resources for other uses. Common solutions include box electors, palletizers, shrink wrappers, and labelers.
To further improve warehouse space utilization, managers might also consider the use of individual task technology solutions as well. Packaging co-bots (robots that perform tasks alongside human operators), large dashboard displays for pick coordination, mobile tablet interfaces to replace paper tickets – anything that can make the warehouse more efficient overall will have space optimization impacts by way of maximizing the throughput of each space type. -
Automated Guided Vehicles (AGV)
-
As our warehouse storage reaches higher densities, we can next look to speed up order fulfillment and provide higher storage position turnover (allowing us to handle more materials in a given period of time and space). Automated Guided Vehicles take manual material transportation out of the equation, saving worker time and optimizing traffic flow free of congestion.
-
Automated Storage & Retrieval Systems (AS/RS)
When storage density and work speed need to be all-out maximized, very advanced solutions known as Automatic Storage & Retrieval Systems are the way to go. Using fully computer-controlled pallet handling and order picking robots, automatic conveyance front-to-back, and software-managed order execution, these AS/RS systems provide the absolute highest amount of storage space and fastest order fulfillment speed (which provides more total storage volume since each storage position turns over faster).
AS/RS systems are almost universally custom-built, one-off solutions. There is no ‘standard offering’ automatic retrieval system. For this reason, the cost and complexity of taking on an AS/RS project will often only make financial sense for very large, very high-volume distribution companies. That said, most smaller distributors can still take inspiration from the virtues of automation storage and retrieval.
First, storage density can be increased with multi-depth pallet racking, but storage sequencing will also need to change to suit (such as going to a First In, Last Out sequence).
Second, a Warehouse Management Software (WMS) package always accompanies an AS/R system, but material handlers can deploy just the WMS on its own to make progress towards highly automated, optimized work plans that humans can still execute.
Third and lastly, a large chunk of the effort in an AS/R project is to automate pallet tracking and identification, which can be achieved on its own by deploying RFID or other wireless technology in order to tap into dynamic positioning without the use of automatic retrieval vehicles.
#designwarehouse #spaceutilization #spaceoptimization #warehouseautomationsystems #warehouselayoutdesign