Getting the Most From Your Kitting or Sub-Assembly Process
Getting the Most From Your Kitting or Sub-Assembly Process
- share
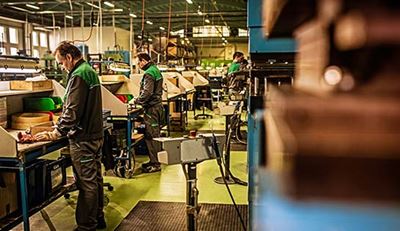
A few questions that you should ask yourself before implementing this process as part of your operation.
An online business dictionary defines kitting as “A process in which individually separate but related items are grouped, packaged and supplied together as one unit”. It goes on to provide examples that include power sources and cords being supplied with electronics, software bundles that are included as part of a technology purchase, products that are grouped together for consumption in a predetermined ratio in a manufacturing process or food products that are combined to create a “new” product made up of several existing SKU’s, such as a gift basket.
The processes behind kitting are usually nothing new – they typically mimic processes that occur on manufacturing floors around the world every day. The interesting challenge is that when these processes occur as part of a manufacturing process or operation, they are usually analyzed, evaluated and measured in very granular detail; however when they happen in a distribution operation, they can be treated as an afterthought, with little regard to best practices, productivity, safety or other key metrics that can significantly impact your bottom line.
If you are running or considering a kitting or sub-assembly process as part of your operation, you will want to make sure that you’ve created a sustainable, repeatable, safe, efficient and ergonomic process. You should begin by asking yourself the following questions:
How long will I be doing this? – This is a key consideration before you start defining any processes. If this is a very short-term commitment to solve an immediate, urgent problem or to help a customer, then it probably doesn’t make sense to analyze or evaluate much investment in infrastructure. If this will be a long-term or ongoing operation, it needs to be set up as efficiently as possible.
Do I have adequate space? – This can be a huge issue. Failing to allocate adequate space for the operation, including staging incoming materials and outbound kits, can result in productivity reductions of up to 50%. One thought to take into the process; kitting operations often work well on or below a mezzanine, so you can often double your “footprint” by duplicating your efforts in the same vertical space.
Do I have adequate lighting? – Lighting is one of the largest single factors that can impact the productivity of your workforce. A well-lit environment is usually viewed as a pleasant, professional and productive work area. Lighting has been shown to directly affect the attitude and morale of associates. When you also factor in the reduced energy consumption (and thus quick payback) of modern high-efficiency lighting, the benefits become even more obvious.
Have I considered ergonomics and employee safety? – While you’d never intentionally put your employees at risk, it’s not uncommon to see kitting operations hastily implemented with little regard for the associates staffing them. You need to put the same level of thought into the work environment and ergonomics that you would anywhere else. To do otherwise is simply inviting trouble.
Have I invested appropriately in automation? – Depending on the complexity of the kitting process and the length of time you’re expecting it to be part of your operation, you should run the calculations on several scenarios to evaluate the ROI on different levels of automation. Your operation may not warrant robotics or laser-guided vehicles, but there could be a more than adequate payback on some conveyor, scanners or a semi-automatic stretch wrapper. Building the infrastructure to do the job correctly and efficiently also shows your associates that you’re taking this part of the business seriously and expect a professional, productive effort.
Have I documented the best practices for my operation? – Like any process in your environment, your kitting operation should have detailed, documented SOP’s that apply to every task in the kitting operation. These SOP’s should be the foundation for training and for any coaching that takes place. They should represent safe, productive, repeatable processes that your associates can utilize.
Do I have a system built in to track my products through this process? – It is important that product moves to and from kitting are tracked the same way and with the same level of timeliness as any other move in your operation. If product in the kitting operation goes into a “black hole” in your inventory or ERP system, it will only be a matter of time until your associates begin circumventing the system by inventing “workarounds” to accommodate the lack of visibility. It could be as simple as creating one WIP area in your inventory system that you move product to, and backflushing components as the kits are created and received into inventory. No matter how you approach it, visibility is critical.
Do I have realistic productivity goals? – There is an old saying that you can’t improve anything until you can measure it correctly. This is absolutely true in any kitting or sub-assembly operation. You need to set productivity goals for your associates that are reasonable and achievable while still being aggressive. Depending on your organizations’ culture, these goals could be based on Engineered Labor Standards, Reasonable Expectancies, Historical Data or some combination of the above.
Are these goals and the results communicated to my staff in a timely manner? – Kitting and Assembly operations are the ultimate in “short memory” work groups. They need to have feedback in almost real-time, so that they have a sense of urgency to make adjustments to their productivity as their work is being completed. You can measure and track any combination of metrics – paid hours vs. units produced, productivity per hour from a specific work cell, quality, accuracy or speed of changeovers. Just make sure that you’ve selected a combination of metrics that allows for constant and timely feedback, preferably at multiple points during a shift.
Have I built in rewards for meeting or exceeding the productivity goals? – Once you’ve got the right metrics in place with timely feedback, be sure that you’ve built in rewards that let your associates benefit from their productivity. After all, if a work team or individual exceeds their production goals, the organization will have very little labor cost tied up in the “plus production”. Sharing some of that benefit with your associates is a great way to create a “win-win” and retain your associates while keeping costs down.
Do I have a plan in place to make sure I don’t overproduce? – Financially speaking, overproducing is a disaster for any kitting operation, as you’ll end up investing labor in breaking down kits, only to be left with the same components you started with and a chunk of additional cost that added absolutely no value to your products. Most world-class kitting operations only build around 70-80% of their projection to stock and build in the flexibility to build the balance on a “just in time” basis.
Have I captured my costs and budgeted/priced accordingly? – Are you accounting for all of your costs in a kitting operation? Have you thought of the labor involved in bringing product to and from the kitting operation? How about those lights that wouldn’t be on if you weren’t kitting? What portion of time do your Supervisors spend dealing with the kitting operation? How about the depreciation on your automation infrastructure? It’s best to involve your Finance folks in this process rather than attempting it yourself.
Should I get a “second set of eyes” onto the kitting operation? – You may be a highly experienced Distribution professional, but unless you also have a Lean Manufacturing background, another viewpoint can be extremely valuable. You can “borrow” some expertise from your Manufacturing group or bring in some outside expertise, but be sure that you get the benefit of other available resources in this process.