Measuring Material Handling Equipment and Systems Productivity and Equipment Costs
Measuring Material Handling Equipment and Systems Productivity Costs
- share
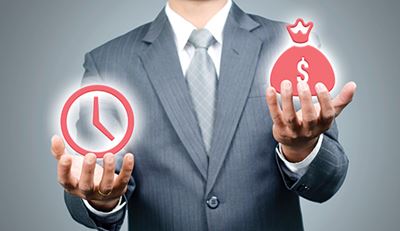
How is your company currently tracking and measuring these metrics? What you don’t know could be costing you money.
More than ever before, companies are looking for ways to drive down costs associated with their material handling equipment and systems. Unfortunately, many of these organizations are focusing solely on traditional cost drivers such as maintenance costs and therefore are missing key opportunities to realize much larger returns.
The first step in determining how to effectively manage your material handling equipment and system’s true costs are to first understand how you are measuring them. Below are four of the most common answers to this question:
- We are not tracking or measuring these costs: Although it may seem surprising this is actually the most common answer, as industry surveys confirm that 94% of companies do not consistently monitor costs associated with their equipment. The good news is that even though this circumstance may seem like the most daunting task, it is actually one of the easiest issues to overcome because you don’t already have a preconceived notion of key metrics. However, it is impossible to manage what you don’t measure. If you do not have any cost history on each piece of equipment, how can you determine if your costs are trending up or down or how do you make equipment replacement decisions? How are you able to understand the productivity of your equipment operators or the equipment that they run? On the bright side there are a number of tools on the market today that can help you gather and consolidate this information. Additionally, there are also a few companies that offer Consulting services to help you get on the right path.
- Our Service Provider is doing this for us: But are they really? A few questions to consider: How regularly are you meeting with your service provider to seek value in the information that they are collecting? Does your service provider only collect this information for the equipment that they are providing service for? Is the information that they provide assisting you with your strategic planning or assisting you with reduction of costs? Have you saved money because of the information that they are collecting? To better understand true cost drivers it is imperative that you are looking at all of the equipment and systems in your fleet to best determine where the cost saving opportunities are.
- Our ERP or Computerized Maintenance Management System (CMMS) is collecting this information: This is a step is the right direction but does your ERP/CMMS collect the proper data to drive improvement in business? If not, can it reasonably be made to do so? Have you devoted an internal champion to pull data into usable reports? Have you devoted time to turning those reports into actions that will reduce costs? Are you only looking at service costs in these models, or are you considering productivity? Many times companies have the correct systems in place to collect this data but lack the internal resources to interpret it and make cost saving decisions based on it.
- We have a formalized Fleet Management Program: Great! This puts you on the path to truly reducing your costs and getting the most out of your equipment and systems. However, here are few questions to ask yourself: Does your program consider all of your equipment and systems within your operation or it is focused on lift trucks? Is your fleet management program yielding measurable results? Are you reducing spending or improving productivity as a result of investment in this program? Are you only looking at service costs in these models, or are you considering productivity? Have you devoted an internal champion to turn your fleet management program into business improvements?
All in all, the importance of tracking, measuring and implementing strategies to reduce the cost and improve the productivity of your fleet has never been more important. Fleet management has grown far beyond basic maintenance reporting. Fleet utilization, enhanced safety practices, performance metrics, energy consumption and replacement schedules are true opportunities which allow companies to maximize financial and operating results. However, you have to first start with measuring these things before you can realize their true benefit.